Process Systems Consulting
PROJECTS
Process Systems Consulting typically is engaged in three particular categories of Projects. These are Process or Incident Reviews for Improvement, Seminars and other Training events, and Process Development Projects (Technical or Systemic).




Process Reviews, Investigations and Audits
1) FDA-Regulated Products: Responsible for program set-up and conformance to FDA operations and documentation standards. Performed pre-FDA inspection audits on a semi-annual basis in three different production locations in the Southeast. All locations successfully passed all FDA inspections without any findings. Worked as an internal consultant in FDA auditing for other related production locations. Reviewed documentation plans and operating procedures for compliance to the FDA regulations.
2) Internal Auditing Training: Trained teams of internal auditors for ISO-9000 audits in a major industrial gas company. These teams consisted of designated Quality Managers and other operations personnel. The training consisted of classroom training in auditing techniques and objectives, and observation of field work. Multiple teams were trained in each production location to provide audits of all areas with independent observers. Trained plant managers in the use of internal auditing for quality improvement as well as compliance with the relevant standards.
3) External Audit of Quality Systems: Served as part of an external audit team for chemical production plant third-party audits. Performed audits to the ISO-9000 standard. Achieved RAB Provisional Auditor status. Developed audit protocols and checklists for independent audits of various production and accounting systems. Performed lead auditor role for Process Safety Management teams in the Southeastern U.S. for six years. Assembled teams of auditors from corporate offices and local plants to provide objective reviews of individual plant operations.
4) Audit Supervision: Acted as lead auditor over a nine year period for specialty gas production operations throughout the U.S. In corporate management I reviewed audit reports and made summary reports to top management with recommendations to the plant management.
5) Audit Liaison: Acted as corporate liaison for third-party audits by registrars and customers. Successfully communicated both the audit findings and intent to the plant management, and the corrective actions and system operation to the auditors. All registrar audit liaisons resulted in successful registration of the audited location without requiring a subsequent visit. Customer audit liaisons resulted in enhanced communication and trust between the supplier and the customer.
6) Supplier Audit: Performed audits of key supplier functions and quality systems for equipment and material suppliers in the industrial gas and specialty gas business. Audits occasionally resulted in the necessary change of a vendor. Most supplier audits enhanced the reliability of the parts or materials supplied, accuracy of billing and efficient shipping. Worked with suppliers on improving the supply chain function to reduce inventory and returned goods.
7) Personnel Training in Quality Systems: Developed and taught basic Quality Systems concepts to plant personnel in a series of week-long seminars. Plant Quality Managers were instructed in more depth, and were assisted in holding monthly special training sessions for plant employees. Fundamentals of statistical analysis, variation, and consistency were taught to all production workers. Line workers were each involved in developing operating procedures and useful record documents. Upper management groups were taught concepts such as process variability, controlled and uncontrolled deviations, the PDCA cycle of improvement, and the absolute necessity of management commitment to resources and support for any successful quality system.
Other significant areas of work have been:
-
Developing statistical analyses and protocols for the efficient production of secondary gas standards for EPA certifications.
-
Automating analytical SPC in a multiple-product high purity gas production and cylinder filling plant.
-
Performing statistical analyses on historical stream analyses over an eight year period to show consistency of a process and to develop ways to improve the product quality.
-
Used statistical analyses to successfully refute claims of off-spec product and demonstrate the error in the external analyses performed.
-
Wrote several technical papers on the use of statistical methods for process control and improvement. Wrote executive summaries on the proper use of quality systems and the effect of excessive adjustment to processes already in statistical control.
-
Analytical development for a major fertilizer company. Initially provided industry survey and sources for the acquisition of rental or purchase equipment to fulfill a specific analytical need. Recommended analytical equipment and procedures. Subsequently contracted to obtain, install, and operate appropriate analytical equipment for the client during pilot operational studies. Project spanned approximately four months.
-
Chemical industry evaluation and description for a major telecommunications firm. Provided specific information on product movements, values, and infrastructure in specialty chemical markets. Assisted in the evaluation of the economic impact of new technologies on current operations. Provided further research for specific market questions generated by the client after initial review of the original survey. Project spanned one month.
-
Assistance in process design for a new source application in carbon dioxide recovery. Provide technical evaluation of design, equipment, and procedures. Assist in process design modifications, safety reviews, equipment evaluation, market valuation and analytical requirements.



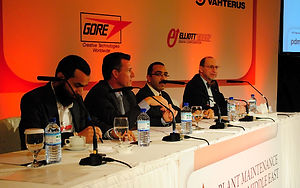
SEMINAR PREPARATION AND DELIVERY PROJECTS
Root Cause Analysis - 2 days
A generic approach is used to avoid the jargon and market of "branded" methodologies. This course focuses on the use of the Human Factors And Classification System to develop an actionable corrective path from an incident to corporate culture. Suitable as a stand-alone procedure or as an aid to your current RCA methodology.
Process Safety Management - 3 days (a 2-day version is also available)
Extensive training seminar developed from original materials, published studies, OSHA regulations, and case studies. This course includes the history of PSM, the regulatory environment, plant safety basics, and sources of information. It continues with a thorough review of the OSHA PSM regulation, the structure of the system, corporate and personal responsibilities, and training and documentation requirements. It concludes with a workshop in hazard identification, procedure generation, performing HAZOPs and maintaining the system. This course has been given numerous times over the last ten years to both corporate level and plant operations personnel.
ISO-9001 Overview and Implementation - 2 days
Seminar developed from original materials and ISO-9001 documents. The first day includes an overview of quality issues and systems in production, distribution, and administration. The development of the ISO standards is presented, and the key attributes are highlighted. The second day includes a detailed study of the ISO-9001 standard, procedure generation, use, and control, internal and external auditing, registrar selection and system maintenance. This seminar has been presented many times over the years, beginning in 1985, with updates as the ISO-9001 standard evolves and more businesses become registered.
Quality Systems for Corporations - 1 day
Seminar developed from original materials to provide a shorter overview of the role of formal quality systems in the profitability of corporations. This seminar includes many of the ISO-9001 seminar elements in abbreviated form, as well as alternative systems and methods of creating a quality culture in a modern corporation. This seminar is presented to management groups that are considering adoption of a formal quality system.
Sterilization and Disinfection - Two Days
International Seminar recently delivered in Singapore for representatives of pharmaceutical, food, and industrial equipment suppliers and clients in Southeast Asia. Developed from current research and regulatory data, this seminar provides training in the classification and control of the four primary biological contamination levels. A combination of lecture and workshops, this course taught mid and upper-level managers how to effectively define and assure the necessary sanitation levels for their operations and customer base.
Contamination Control – Two Days
International Seminar for representatives of Manufacturing Pharmaceuticals, Biopharmaceuticals, Nutraceuticals & Medical products and clients in Southeast Asia. Developed from current research and regulatory data, this seminar provides training in the the implications of the ISO International Standards & Regulatory Guidelines for FDA and EU Good Manufacturing Practice Compliance. An understanding of the implications of FDA & EU Harmonization is also developed. A combination of lecture and workshops, this course taught mid and upper-level managers how to effectively define and control contamination sources and mitigation requirements.
Other Seminar courses include:
Statistical Process Contro
Project Management
Process Instrumentation
Analytical Systems
Basic Process Control
Gas Chromatography
Refrigeration in Transport
Microcontamination Control through Advanced Cleaning
Contamination Reduction through SPC in Production
Laboratory Safety I
Laboratory Safety II
Technical Consulting Projects
Development of a delivery system for the addition of a trace additive to a bulk stream.
Problem: The client required a small amount of a binding material to be added to a large amount of product before processing. This binder needed to be added to prevent final product crumbling or breaks, resulting in rejected material. Excess binder addition results in poor product acceptance due to texture and residual material in the product. This product was delivered in batches as part of a continuous pressing operation. Precise addition of the additive was required, with the potential to adjust the rate within certain parameters. A high pressure and temperature gradient was required due to the nature of the product.
Solution: Process Systems Consulting utilized a precision metering pump system that was capable of producing the required small precise flows of the liquid additive from ambient conditions into the high pressure and low temperature process fluid. Proper mixing and distribution of the additive was accomplished by the design and placement of the delivery orifice at a proper point in the product delivery system. This was done through dynamic flow analysis of the process stream and automated timing mastered at the production unit control center.
Results: Multiple units were installed on presses in various production locations. Units run with minimal maintenance 10-24 hours per day, 6 days per week. Blending is consistent from batch to batch, and from machine to machine, resulting in predictable and consistent final product composition. Product losses from breakage were reduced by 15-20% while maintaining acceptable texture and residue levels.
Design of a Precision Gas Blending System.
Problem: The client required a device to accurately and repeatably deliver variable concentrations of gas blends to process equipment. It was desired to use only pure gases or percentage-level blends of the desired components in order to reduce the cost and delivery time of the final blends. Commercial devices were considered too expensive and incapable of handling some of the reactive gases required by the client.
Solution: Process Systems Consulting designed a cascade blending system with existing mass flow control systems that permitted on-demand generation of standards accurate to 1.5% and traceable to NIST from pure gas and 1-5% gas blends. A specific advantage was the proprietary development of a unique micro-blending nozzle, which allowed the complete and rapid mixing of the gases for consistent final mixtures in a very short flow path. Steven Cooke did the nozzle design and construction.
Results: Multiple units were built and distributed to the client's major specialty gas production facilities. The units were built at a cost to the client of 50% of the available commercial units, and included the ability to handle reactive and corrosive materials - a property that was not available in the other commercial units. The scalability of the system allowed each unit to replace dozens of expensive trace-level gas standards with a few high-purity gas supply cylinders.
Development of a blending system for the addition of small amounts of a reactive material to a process stream.
Problem: The client required a precise amount of a coating additive to be added to a gas stream flowing into a continuous reactor. This additive needed to be added in precisely variable amounts to generate different coating thicknesses on a final glass product. The combined stream was delivered continuously through the coating reactor. Precise addition of the additive was required, with the ability to adjust the rate accurately and repeatably.
Solution: Process Systems Consulting utilized a precision liquid syringe with a direct gear-driven injector to accurately add the additive in precise and variable amounts to the main reaction gas stream. The injection rate was calculated to not exceed the vaporization rate and partial pressure constraints of the additive, and the syringe type and size was determined by the required final blending accuracy requirements and the normal process run time. Blending results were confirmed and tracked with a process gas chromatograph until the system was accepted as reliable.
Results: Rapid changes in coating composition were possible with little downtime. Reactive materials were safely handled and controlled with no worker exposure. The production process could be carried out in an effective and efficient continuous manner. Difficulties of pre-blended mixes and storage stability problems were eliminated. Batch to batch consistency of the final coating was improved.
Gas Mass Transfer Operations.
1) Problem: Minimize consumption of reactant gas (carbon dioxide) while maximizing effect (pH control) in a variety of geometries (mixed tank, effluent weir, open reservoir).
Existing Technology: Open tube spargers of varying geometries placed in the liquid streams, flow controlled by fixed setpoint and periodic downstream sampling and testing of the stream.
My Improvement: Examined stream flow rates, temperatures, and pH fluctuations over time. Determined minimum theoretical CO2 consumption from dual-endpoint (buffered) calculations. Calculated optimum contact time for mass transfer from gas to liquid phase, with reaction. Designed sparger specifications and location to maximize utilization of the CO2 with minimum stream disruption. Added on-line pH controller to regulate CO2 flow.
2) Problem: Effective removal of toxic gases (PH3, WF6, HCl) from reactor effluents.
Existing Technology: Burning or direct reaction in caustic bath.
My Improvement: Dissolution of acid gases into a water bath, followed by pH-controlled neutralization with basic solutions. Design of gas sparging system (lab scale) to provide sufficient contact times and heat rejection to handle normal and emergency flow rates. Reaction of PH3 directly into a KMnO4 solution to minimize toxic releases and generate a disposable effluent. Calculation of PH3 dissolution and KMnO4 reaction to provide sufficient reactive volume and excess of process upsets.
3) Problem: Dissolved gas removal from liquid streams for high purity applications.
Existing Technology: Boiling, or phase separators.
My Improvement: Use mass transfer of trace dissolved gases from the liquid phase into an inert, non-soluble gas, followed by disentrainment from the liquid. Determine optimum flow rates for a given contact time, average bubble size, and desired purity level using nitrogen or helium at the sparging gas.
4) Problem: Methanol removal scrubber was not operating according to design specifications.
Existing Technology: Vendor had used a proprietary "special" packing with claims of higher efficiency.
My Improvement: Made calculations based on actual operation to demonstrate the inefficiency of the packing. Calculated required mass transfer rate for the existing column dimensions and product flow rate and found a suitable packing to achieve that rate. New packing was obtained, and the removal efficiencies exceeded the design specifications by 20%.
5) Problem: Removal of large amounts of H2S from a CO2 stream.
Existing Technology: MEA and MDEA solvents. Co-adsorption of CO2 made them very inefficient. Operating costs were too high to permit the use of some streams.
My Improvement: Developed a continuous removal system using reversible absorption of H2S into an iron chelate compound. Solution was non-reactive towards CO2, could remove significant amounts of H2S, and operated at a lower cost than MDEA systems. This process was subsequently patented by ARI Technologies for commercial applications.
6) Problem: Efficient separation of air and hydrocarbons from carbon dioxide for recycling of stripper vent gases.
Existing Technology: None - vent gas was not recovered.
My Improvement: Helped develop fixed membrane technology using commercially available membranes to effectively enrich the CO2 stream to a useable level. This work initially required a great deal of calculation of the relative diffusion rates of the various gases, the resultant mass rates and purities. Computer simulations were first designed to calculate the preferred mix of membrane properties. Subsequent pilot tests were done to refine the models and develop commercial applications. All three major industrial gas companies now offer a variation on this method.
7) Problem: Develop uniform coating technologies for glass modification.
Existing Technology: Liquid or spray coating followed by annealing, or incorporation into the bulk glass, which is too expensive.
My Improvement: Directed the team charged with developing a gas-phase coating process on finished glass to generate precise but variable thickness coatings of metals. My direct involvement was in the design of the reactor vessel to provide a laminar flow region over the sample, minimize reactant losses, and provide precise temperature and contact time control. Experiments were also modeled by finite element analysis.
Other significant project areas include:
-
Gas cylinder preparation, where the application of diffusional principals obtained the optimum method of preparing ultra-high purity cylinders with respect to residual moisture (it is a function of the physical dimensions and the orifice size - not the delta-P).
-
Gas and liquid sampling and stability for analysis, in which phase separations and relative solubilities and vapor pressures make a significant impact on the type of method required.
-
Impurity migration in bulk systems, including storage vessels, transports, and transfer systems.

